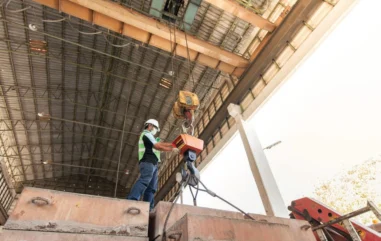
From oilfields and offshore rigs to construction sites, shipyards, factory floors and even farms, lifting equipment is the backbone of heavy operations. Yet every hoisted load carries significant risk. Whether it’s a suspended pipe on an oil rig, a swinging steel beam on a construction site, or a hay bale lifted on a farm, the consequences of a mishap can be catastrophic.
In North America, crane-related accidents average roughly 42 fatalities per year, and a ten-year study of 249 crane incidents recorded 133 injuries and 133 deaths, with nearly 37% of incidents resulting from workers being crushed by swinging or dropped loads. These sobering numbers underscore a simple truth: regardless of the industry, safe lifting practices are literally a matter of life and death.
The hidden dangers in every lift
Each industry faces its own lifting challenges, yet some risks are universal. Human error and improper use of equipment top the list of causes for lifting accidents. Poor rigging techniques can lead to dropped loads; miscommunication among crew members can result in dangerous swings. For example, one study found that 27% of crane accidents involved dropped loads, often stemming from inadequate rigging practices. Environmental factors also play a critical role.
Construction cranes must contend with high winds, maritime and offshore lifts deal with vessel movement and weather, and agricultural or mining operations often face the challenge of uneven ground. Overloading equipment, using the wrong gear, or ignoring hidden defects can lead to catastrophic failures.
Real-world incidents drive these points home. In August 2023, an uncertified crane operator in Florida was assigned alone to lift roof trusses at a construction site – a task for which he was neither trained nor supervised. During the first lift, the crane’s cable contacted overhead power lines, electrocuting the 34-year-old operator. OSHA investigators later noted that the employer had “cut corners and made the conscious choice to send an uncertified crane operator to a job site”, a decision that proved fatal.
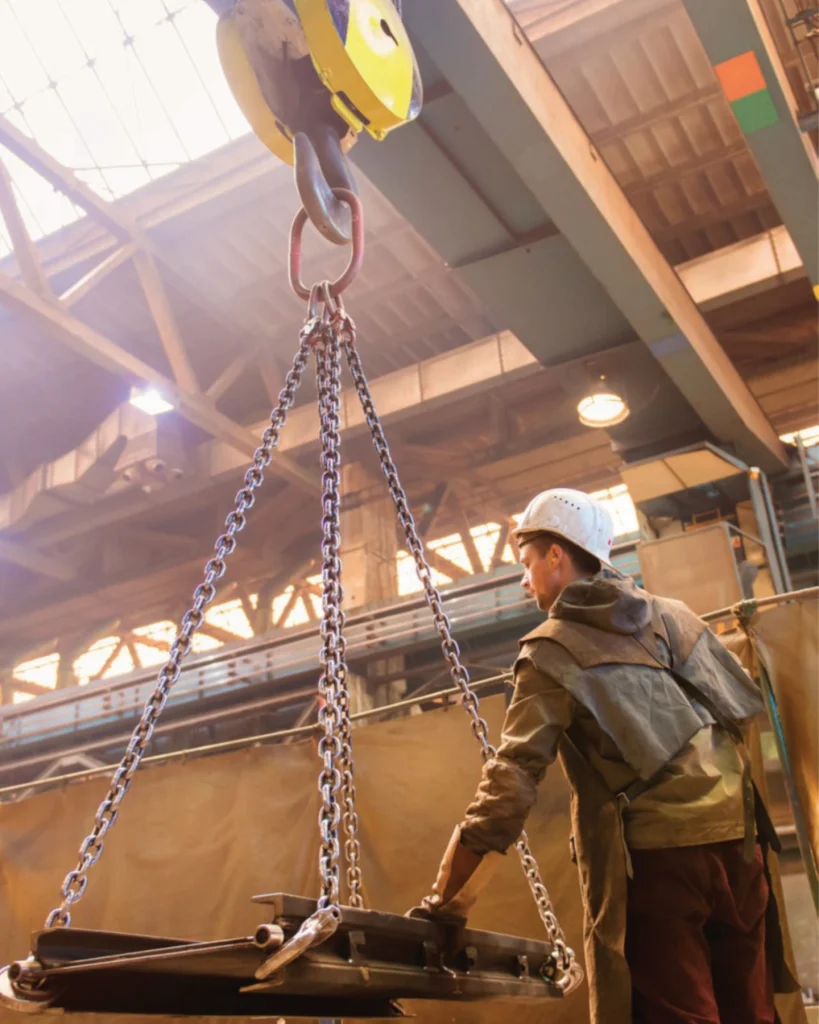
The company was cited for multiple serious safety violations: failing to stabilise the crane, allowing work too close to power lines and not ensuring the operator was certified. This tragedy is a stark reminder that every shortcut in lifting operations can carry a heavy price. Whether it’s a collapsed crane, a dropped container in a port or a hoist failure in a factory, the root causes tend to be the same: lack of planning, inadequate training, poor equipment upkeep or a breakdown in safety culture.
Lift plans: roadmaps for safety
One of the most powerful tools in any lifting operation is a well-crafted lift plan – a detailed roadmap that outlines how the lift will be conducted safely. In many jurisdictions, such as under UK regulations, having an adequate lifting plan is a legal requirement for complex lifts. For routine operations, a general plan may suffice, but for special or complex lifts, a specific written plan is mandatory.
A good lift plan must address three key questions: what is being lifted? Who is involved? And how it will be done safely? This planning process forces the team to visualise the entire lift, from start to finish and identify potential problems on paper rather than mid-operation. As the saying goes: “Plan the lift and then lift the plan.”
In practice, crews that take lift plans seriously tend to execute lifts more smoothly and confidently. Working out potential issues in a meeting or on a whiteboard is far preferable to attempting on-the-fly fixes when a load is already swaying dangerously overhead.
Pre-use inspections: your first line of defence
Even the best lift plan can be undone by a simple equipment failure. That’s why pre-use inspections are non-negotiable in safe lifting operations. Before any crane, hoist, sling or shackle is used, a competent person should perform a brief but focused inspection to catch any obvious defects or misconfigurations.
For example, a mobile crane operator will inspect the crane for leaks, loose pins, damaged tyres or outriggers and verify that limit switches and safety devices are functioning correctly. They also check the load chart and ensure the crane is properly set up, with outriggers fully extended.
When it comes to lifting gear like slings, chains or eyebolts, riggers look for cuts, fraying, bent links, cracks or excessive wear. Even for forklifts or telehandlers, operators must inspect critical components like forks, brakes and steering systems. Any equipment that fails these checks must be taken out of service immediately – a small catch now can prevent a catastrophic failure later.
Regular pre-use inspections are often mandated by company policy or regulations because they work so effectively in hazard prevention. A simple observation – such as noticing a missing hook latch or a misaligned shackle pin – can stop a chain reaction of failures. Routine inspections not only prevent accidents but also instil a sense of ownership and discipline among workers regarding the equipment they use, reinforcing that safety is an everyday practice.
Certified examinations: don’t skip the check-up
Beyond the daily inspections carried out by operators, lifting equipment requires periodic, thorough examinations by certified professionals. Think of these examinations as scheduled maintenance check-ups for a vehicle – but with much higher stakes. Regulatory bodies around the world call for thorough examinations at regular intervals. In the US, OSHA and Canadian standards often require annual inspections for cranes, while the UK’s LOLER regulations mandate exams every 6–12 months depending on the equipment.
Engaging a certified third-party provider for these examinations is best practice. An independent, qualified inspector can identify issues that in-house personnel might overlook due to familiarity or production pressures. During a thorough examination, inspectors assess critical components, test safety systems and review maintenance records.
Techniques such as non-destructive testing – magnetic particle or ultrasonic tests – are employed on crane hooks or load-bearing welds, and inspectors verify the calibration of load indicators and the integrity of wire ropes. They also ensure that all markings and documentation, such as the “birth certificate” of the equipment, are in order. Should any component be found unsafe, the equipment is immediately flagged for repair or removal from service.
The value of these examinations cannot be overstated. They offer a deep dive into the equipment’s health that goes far beyond what a daily visual inspection can achieve. For instance, a wire rope might appear fine externally but could have internal corrosion detectable only through a professional examination.
Similarly, an inspector might find that a critical pin on a crane was replaced with an incorrect grade bolt, or that an unreported overload incident left subtle deformations. Such findings not only help prevent accidents but also provide companies with the opportunity to fix issues and extend the life of their equipment. Documentation of these examinations is also essential for regulatory compliance, helping companies avoid legal penalties and demonstrating due diligence.
The LEEA code of practice: a global framework for safety
The principles of planning, training, maintenance and inspections are not just common sense – they are codified in leading guidance documents such as the Lifting Equipment Engineers Association’s (LEEA) Code of Practice for the Safe Use of Lifting Equipment, commonly known as COPSULE. LEEA, recognised globally as an authority on lifting, has established Section 1 of COPSULE as the educational framework that underpins safe lifting practices worldwide.
Section 1 of COPSULE sets out five fundamental pillars of safe lifting:
- Planning: Operations must be adequately planned and supervised.
- Training: Personnel involved in lifting operations must be properly trained.
- Maintenance: Equipment must be maintained in safe working condition.
- Inspection: Equipment must be inspected and thoroughly examined to ensure it is safe to use.
- Documentation: Proper records of tests, inspections and examinations must be kept.
These pillars reflect decades of industry experience, and the lessons learned from numerous accidents. By adhering to the COPSULE framework, companies build a safety net that catches potential issues long before a lift begins. LEEA’s guidance is comprehensive, authoritative and globally applicable – helping to ensure that best practices in lifting become standard practice in every operation.
Making safe lifting second nature
The goal for any industry is to make safe lifting an instinctive part of daily operations – a culture where every worker knows that safety is paramount. When a company achieves this, visitors to the site immediately notice the difference. Operators conduct pre-lift toolbox talks and equipment checks without prompting, managers routinely discuss lift plans during project meetings, and everyone knows who the competent authority is when questions arise. In such a culture, even near-misses and minor issues are reported and analysed, rather than hidden or ignored.
Creating this safety culture requires a commitment from all levels of the organisation. Workers must feel empowered to voice concerns and even halt a lift if something seems unsafe, with the assurance that management will back their decisions. This kind of environment not only reduces accidents but also boosts efficiency and worker morale. Lifts that are well-planned and executed result in fewer breakdowns and less downtime, ultimately saving time and money.
Organisations in North America and around the world can leverage the extensive knowledge offered by LEEA and similar bodies. By adopting the LEEA COPSULE guidance, training staff to LEEA standards and using LEEA-member inspectors and suppliers, companies can integrate international best practices into local operations. The tragedies and statistics discussed earlier are not an inevitable cost of doing business; they are preventable through disciplined application of proven safety principles.
Safe lifting is about more than compliance or avoiding fines – it is about protecting human life. Every operator, rigger and bystander deserves to return home safely at the end of the day. Whether working on a drilling platform in the Gulf of Mexico, a high-rise construction site in New York, a port in Houston, or a farm in the heartland, safe lifting practices ensure that no load is worth risking a life.
Lifting equipment wields immense power – to build, to move and to transform our world. Harnessing that power safely, with a steadfast commitment to excellence at every level, ensures that best practices become standard practice and that “safety above all” is more than just a slogan. It is a daily reality that upholds the reputation of our industries as responsible, forward-looking and fundamentally safe.
Ensuring the safety of lifting operations is paramount across various industries including oil and gas, construction, maritime, offshore and manufacturing. The challenges of lifting operations are multifaceted, but the principles remain the same: thorough planning, rigorous inspections, certified examinations and adherence to internationally recognised standards such as those set by LEEA. When companies invest in these practices, they not only protect their workers but also improve efficiency, reduce downtime and safeguard their reputations.
By integrating robust lift plans, conducting daily pre-use inspections and scheduling periodic certified examinations, organisations can mitigate the risks inherent in lifting operations. LEEA’s Code of Practice provides a global framework that encapsulates these principles, guiding companies towards higher safety standards. With LEEA’s support and resources – from training and technical guidance to certification and audits – safe lifting can indeed become second nature in every industry.
Ultimately, every effort made towards ensuring safe lifting practices is an investment in human life. The goal is clear: no matter the industry or the scale of the operation, nothing is worth the loss of life. As companies continue to adopt best practices and foster a culture where safety is embedded in every operation, they contribute not only to their own success but also to a broader, global effort to eliminate lifting accidents, injuries and fatalities.
Safety in lifting operations is a collective responsibility that demands meticulous planning, diligent inspections and a steadfast commitment to continuous improvement. By aligning with best practices and adhering to the standards set by authorities like LEEA, every stakeholder – from the operator on the ground to the executive in the boardroom – plays a crucial role in ensuring that each lift is executed safely. This is the path towards a future where best practice becomes normal practice, and safety is never compromised.
In embracing these guidelines, industries worldwide can transform the inherent risks of lifting operations into manageable challenges, ensuring that every load, whether heavy or light, is lifted with the care and precision necessary to protect lives and maintain operational integrity.
LEEA: Leading the way in lifting safety
In the realm of lifting safety, LEEA stands as a global thought leader and trusted authority. Founded over 75 years ago in the UK, LEEA has grown into a worldwide membership body representing companies and professionals across North America, Europe, Asia, the Middle East and beyond. Its influence is such that LEEA membership is often seen as a mark of quality and safety by end users. A LEEA-certified inspection certificate or contractor’s credentials serve as a shorthand assurance of high standards.
Membership with LEEA involves rigorous audits and a commitment to excellence. Prospective member companies must demonstrate competence in staff training, inspection procedures, and safety management before being accepted. Once accredited, members undergo regular audits – including unannounced spot checks – and are required to continually improve their practices. This ongoing commitment ensures that LEEA member inspection firms use the latest methods and maintain up-to-date training, while lifting equipment suppliers adhere to evolving safety standards and regulations.
For organisations that operate lifting equipment – whether in oil and gas, construction, ports or manufacturing – LEEA membership offers a strategic pathway to improved safety and regulatory compliance. Corporate members and companies engaging LEEA services benefit from a wealth of resources, including training courses (both in-person and online), technical guidance and safety alerts on emerging issues. These services help organisations elevate their safety practices and ensure that every lift is conducted with the utmost care.
Moreover, LEEA works closely with regulatory bodies and standards organisations worldwide. Its experts participate in committees that shape international standards, influencing guidelines such as ISO standards, ASME B30 in the US and CSA standards in Canada. When companies follow LEEA recommendations, they are not only enhancing safety but also aligning with the same language and requirements as regulatory authorities. As LEEA CEO Ross Moloney stated during Global Lifting Awareness Day 2023, “Remember that LEEA exists to eliminate lifting accidents, injuries and fatalities, [as well as to] educate, influence and enable so that best practice is everyday action.”